Preform coating lubricant significantly improves bottle quality and appearance.
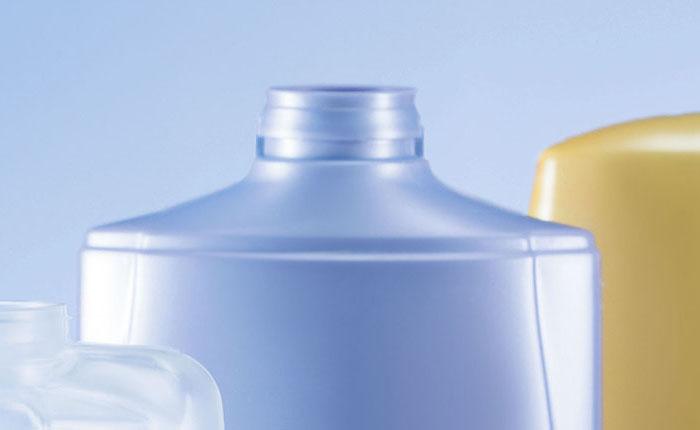
Case Study Thermoplastics:
Lusin® lubricant offers multiple benefits throughout the entire process, from producing preforms and transporting them to blow moulding the finished cosmetic bottles
WHAT WE ACHIEVED.
A global packaging manufacturer producing PET preforms and bottles for a premium brand cosmetic company was dealing with significant rejects due to quality issues. Not only did the oval shape of the bottles often cause blockades in the conveyor belt, but a considerable amount of final blown bottles did not pass the quality check due to scratches, insufficient surface gloss level, and deviating geometrical tolerances. To solve these issues, the manufacturer sought Chem-Trend’s support given our technology and expertise in thermoplastics processing.
Lusin® Lub O 32 F lubricant was tested and found to deliver superior results against the competitive products. Together, the manufacturer and Chem-Trend’s thermoplastics specialist evaluated and defined the correct application of the Lusin® lubricant to sufficiently reduce quality issues and improve production efficiency. As a result, the manufacturer was able to increase their production throughput by 5% while also benefitting from another 5% reduction in rejected bottles due to surface scratches. An additional benefit was seen in transportation where Octabins could hold an extra 15% of preforms.
HOW WE GOT THERE.
From the manufacturing of PET preforms in one location to the labeling and filling of blown bottles in another location approximately 350 km away, Chem-Trend’s regional thermoplastics experts visited the production sites and observed every step of the process to identify solution-critical parameters.
Preforms that were not steadily coated with lubricant resulted in preforms sticking, which generated scratches during handling and transportation and affected the gloss of bottles when blown. The sharp angles in the PET bottle geometry also complicated the production process (e.g., bottle to cap shoulder adjustment, see below illustrations) and the discharging of bottles from big bags created a lag in production.
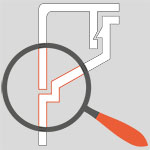
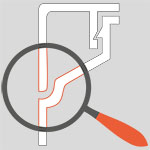
Due to the oval shape of the bottles, blockades in conveying curves were frequent, and electrostatic charge caused by friction complicated the labeling process by causing bends or creating air bubble defects in the filling station.
To improve the coating process, the manufacturer developed a machine capable of coating micrograms of pure, undiluted lubricant on the external surface of single preforms. When used in this machine, Lusin® lubricant allowed for a massive reduction in terms of microbiological growth so that the cleaning cycles of the spray system could be significantly reduced by 77% compared to the previous water-based solution.
OUR SOLUTION.
We helped simplify and establish a repeatable coating process through use of Lusin® Lub O 32 F lubricant on millions of preforms per year. The natural sticking of PET material was counteracted by applying only a fraction of a gram on PET preforms right after their production on injection moulding machines.
From Octabins on the production floor to the labeling of finished bottles hundreds of kilometers away, the entire process benefitted from more preforms per delivery, better blowing of geometrically complicated preforms into bottles, faster emptying of big bags full of blown bottles, less blockades into conveyor belts, faster production throughput, and easier labeling.
Lusin® Lub O 32 F requires no dilution with deionized water and is very resistant to microbiological growth, which directly contributed to the reduction in cleaning frequency for the spray coating machine by 77%.
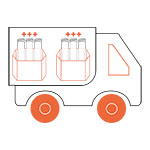
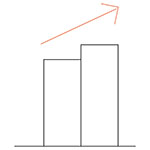
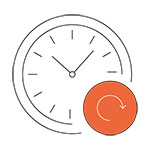
DATA INSIGHTS
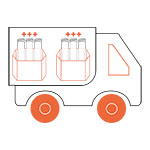
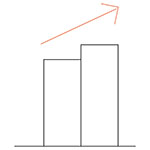
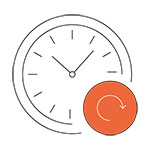
HANDPRINT IMPACT
At Chem-Trend, we pride ourselves on our long history of sustainability efforts. However, it is our effect on our customers’ processes that provides the greatest impact. It goes beyond our global Footprint; it is our even wider Handprint.
Here, we achieved the following:
- Elimination of scratches on preforms – fewer rejects, better gloss of final bottle, easier labeling.
- Reduced transportation costs and reduced CO2 footprint through fewer shipments.
- Reduced water use – no water needed for dilution of lubricant – resource conservation.
- Reduced capacity for microbiological contamination through water dilution.
- Extended the cleaning cycles of spray equipment.
- Reduced number of blockades in conveyor contributing to higher production throughput.
Materials
Waste
Energy
Emissions
Water
